Supported by GM LEP investment, Greater Manchester is working to unlock the potential of graphene and other 2D materials. James Baker is Chief Executive of Graphene@Manchester, which leads business-facing development of graphene and 2D materials at The University of Manchester. Graphene@Manchester includes the National Graphene Institute and Graphene Engineering Innovation Centre. Here Baker talks about the potential for graphene to drive the sustainable transport revolution.
The aerospace and auto sectors are having to respond to two unprecedented global crises – COVID-19 and climate change.
The COVID pandemic has decimated international air travel and so impacted the aerospace industry, which is now forced into making huge layoffs. The situation is just as challenging for carmakers in many parts of the world.
These industries now have a make-or-break opportunity to use the COVID challenge as a catalyst to accelerate the innovation cycle and, in doing so, look to become more sustainable and greener sectors.
This is prompting a drive to have more environmentally friendly vehicles by the mid-2030s – to do that, we’ll need to move away from conventional fuel-guzzling and polluting engines into, say, hydrogen or electric hybrids in the case of aircraft and most certainly electrification for automobiles.
Vehicles of the future will also need to be lighter in weight so they can have longer range, while using less fuel, producing less emissions and generating less noise.
Graphene and 2D materials can play a key role in supporting this huge ambition to produce greener aircraft and cars by the mid-2030s. But manufacturers and their respective supply chains will have to operate very differently than they have done traditionally.
Material Acceleration
If I focus on the aerospace sector – the industry where I started my own career – I would say that historically innovation in materials, for example carbon fiber, has taken many years from discovery through to prototype, through to production, through to mass production.
Post-COVID we will all have to do things differently and there is now a real opportunity to adopt revolutionary advanced materials by working closely with the aerospace supply chain and operate in a much more aggressive ‘make or break’ way.
For example, we can add graphene into a composite to see how we optimise that mix. If our experiments fail, then we ‘fail fast, learn fast’ – that is, we discover quickly what went wrong, fix it and move on quickly to drive rapid innovation.
We cannot underestimate the challenges ahead – but I can see some real opportunities here and the aerospace sector is now likely to be a pioneer and early adopter when once it was very conservative in embracing new technology at pace.
This fast-track pathway was already being laid out. A couple of years ago I helped produce a strategy paper with the Aerospace Technology Institute (ATI), which is responsible for the technology strategy for the UK aerospace sector.
Collaboration across the supply chain
Even before COVID, we recognised the need for restructure to meet the global environmental challenges. The ATI-Manchester joint INSIGHTS paper was produced in consultation with a range of stakeholders and highlighted the potential of graphene to positively impact on aircraft performance, cost and fuel efficiency.
The recommendation was to work with the existing supply chain to incorporate graphene into materials already used to build planes. The collaboration between industry and academia was cited as being crucial in the R&D ambition.
And this industry-academia partnership is exemplified with how the Graphene Engineering Innovation Centre (GEIC) – the graphene commercialisation accelerator based at The University of Manchester – is working with some of its key commercial partners including GKN Aerospace and Versarien.
GKN Aerospace – one of the world’s leading suppliers of manufacturing to the aerospace industry – is working with Manchester to explore multiple areas of 2D materials application, including the use of graphene in innovative coatings for aerospace applications and development of new composite materials.
GKN supplies products to 90% of the world’s aircraft and engine manufacturers, so we have an opportunity to make a genuine difference to the next generation of lighter, more sustainable aircraft through innovation in 2D materials.
Meanwhile, Versarien, like GKN a Tier 1 partner of the GEIC, is working with Manchester on a project with Rolls-Royce as part of a programme to help apply graphene and other 2D materials into next-generation aerospace engine systems.
Lower costs and emissions
The companies will seek to use the unique properties of these advanced materials to reduce the weight of electrical components, improve electrical performance and also increase resistance to corrosion of components in future engine systems – so lowering cost, as well reducing energy and engine emissions.
In these case studies the GEIC, with its ‘fail fast, learn fast’ philosophy, is providing the catalyst to these companies as they look to pull innovation though the aerospace supply chain. And this acceleration can just as easily be applied to the automotive supply chain, which in fact, often overlaps with the aerospace ecosystem as their manufacturing needs are similar.
This Manchester model of materials innovation, I believe, could provide the answer to the aero and auto sectors as they respond effectively to COVID and become fit-for-purpose in a world that will demand sustainable manufacture and products.
This article has previously appeared on investinmanchester.com.
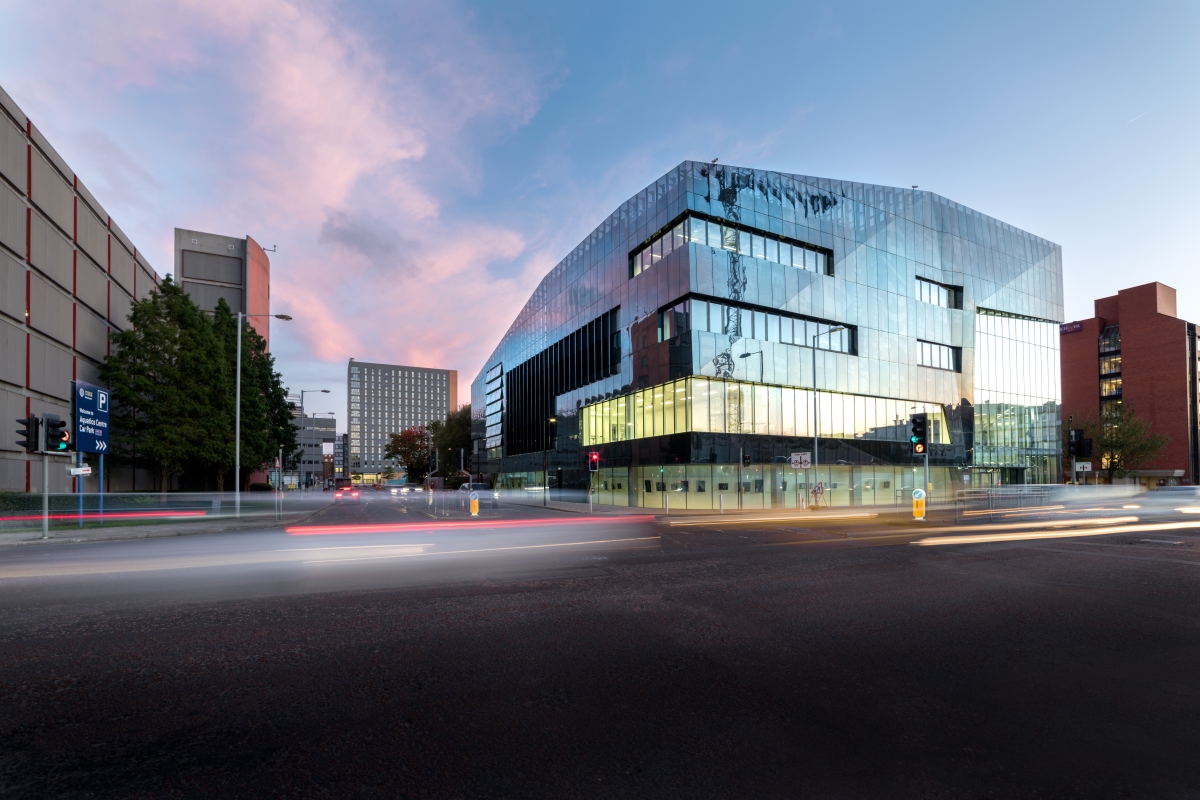
National Graphene Institute
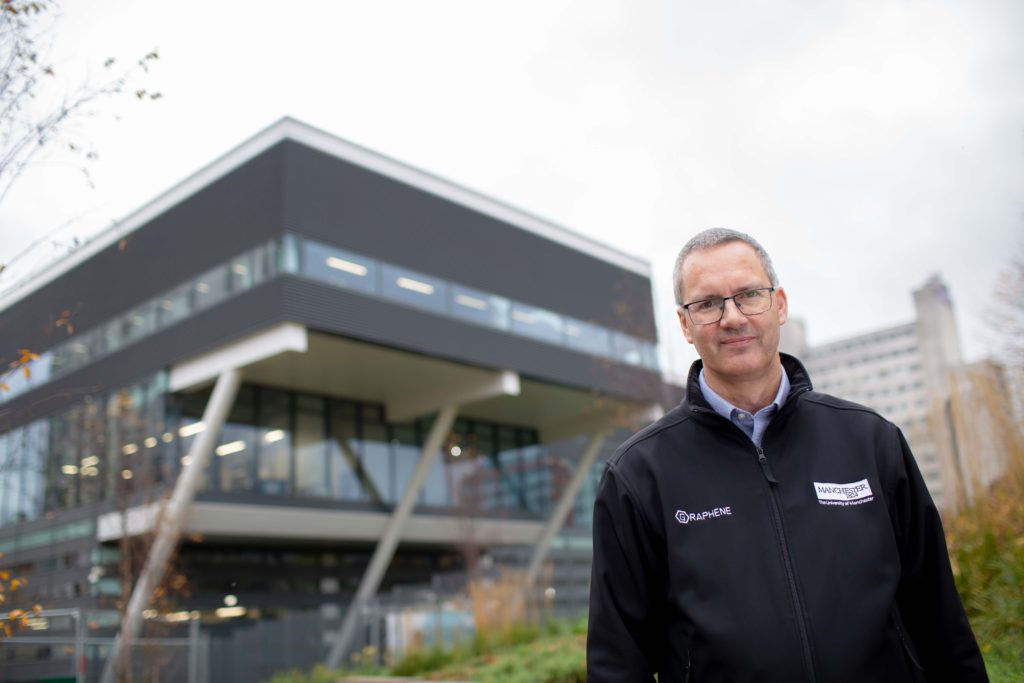
James Baker, Chief Executive of Graphene@Manchester
Inside the Graphene Engineering Innovation Centre